The Use of Cement in Modular Construction Systems
01.07.2025
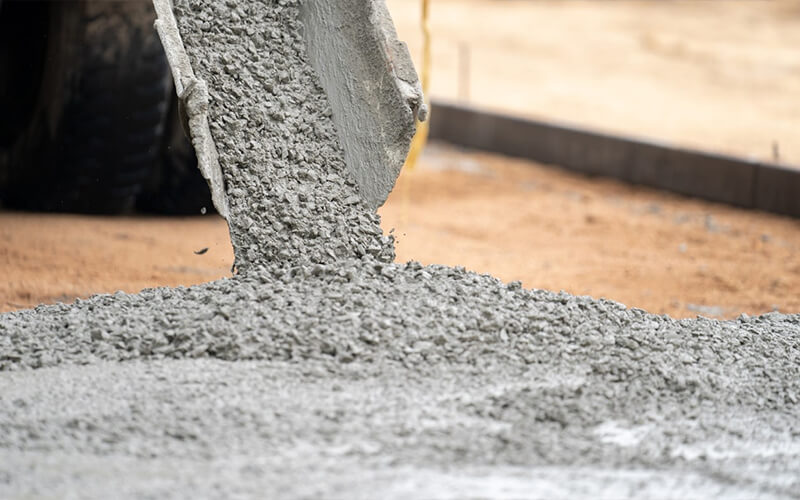
Modular construction is rapidly changing the face of the building industry, offering faster, cleaner, and more efficient ways to create everything from homes to hospitals. As this trend grows, cement-based materials are playing a critical role in enabling strong, durable, and fire-resistant modular structures. By blending traditional construction materials with cutting-edge off-site techniques, cement contributes significantly to the evolution of modular building systems.
While modular construction is often associated with steel and timber, cement is proving to be an essential component due to its structural reliability, energy performance, and flexibility. This article explores the various ways cement is used in modular construction systems and how it contributes to building speed, sustainability, and long-term performance.
Understanding Modular Construction
Modular construction involves manufacturing building components, or modules, in a factory-controlled environment and then assembling them on-site. This method reduces construction time, minimizes waste, and ensures a consistent level of quality. The prefabricated modules can include walls, floors, ceilings, and even entire rooms.
The structural framework of these modules can vary depending on the design requirements. Cement-based materials such as concrete panels, cement boards, and precast elements are often chosen for their durability and thermal performance. These materials also meet rigorous fire, acoustic, and environmental standards, making them ideal for modern modular projects.
Key Applications of Cement in Modular Systems
Cement plays a diverse and foundational role in modular construction. Below are the most common applications where cement-based materials are used:
1. Precast Concrete Panels
Precast concrete panels are manufactured in a controlled factory setting and then transported to the site for assembly. These panels form walls, floors, and façades, offering exceptional strength and dimensional accuracy. Precasting also allows for greater design flexibility and reduced on-site labor.
2. Cement Boards and Panels
Cement boards are widely used in modular interiors and exteriors. They provide moisture resistance, fire protection, and a sturdy substrate for finishes. Fiber cement boards, in particular, are lightweight yet strong, making them ideal for modular wall systems and façade cladding.
3. Structural Concrete Modules
Entire room-sized modules can be cast from reinforced concrete, including plumbing, electrical systems, and finishes. These "volumetric" modules are then transported and stacked on-site. Cement allows these large modules to maintain structural integrity during lifting and transport.
4. Lightweight Concrete Elements
For certain applications, lightweight concrete is used to reduce the load on structural supports and foundations. These elements are often made using expanded clay, pumice, or foam beads. They maintain thermal insulation while offering adequate compressive strength.
5. Cementitious Grouts and Binders
During modular assembly, cement-based grouts and binders are used to seal joints, anchor modules, and enhance structural cohesion. These materials are engineered for rapid setting, allowing for quicker installation and less downtime.
6. Foundation Systems
Even in modular projects, cement is essential for foundations. Precast concrete footings, pads, or slabs ensure stability and longevity. They are often installed before modules arrive on-site to streamline assembly.
7. Flooring and Subfloor Systems
Cementitious screeds and subfloor panels provide a smooth, durable base for various flooring finishes. These materials are used both in the factory and on-site to ensure even surfaces and thermal mass benefits.
Advantages of Using Cement in Modular Construction
Integrating cement into modular construction yields multiple benefits that align with modern building demands. Here are the most notable advantages:
- Speed: Precast and prefabricated cement components accelerate construction timelines by minimizing on-site work.
- Strength: Cement provides high compressive strength, making modules safe for stacking and long-term use.
- Fire Resistance: Cement-based materials are inherently fire-resistant, contributing to building safety and code compliance.
- Acoustic Insulation: Cement panels reduce sound transmission, improving privacy and comfort in modular environments.
- Thermal Performance: Cement offers thermal mass, which helps regulate indoor temperatures and reduce energy use.
- Low Maintenance: Cement surfaces are durable, resistant to pests and mold, and require minimal upkeep.
- Sustainability: When made with recycled aggregates or alternative binders, cement can contribute to green building certifications like LEED.
Innovations in Cement for Modular Applications
The cement industry is responding to the demands of modular construction with new technologies and formulations. Key innovations include:
- Ultra-High-Performance Concrete (UHPC): Offering exceptional strength and durability, UHPC enables thinner panels and more compact modules.
- 3D-Printed Concrete: Some modular builders are adopting additive manufacturing with cementitious materials to create intricate, customized components.
- Geopolymer Concrete: A low-carbon alternative to traditional cement, geopolymer materials are being tested for use in prefabricated modular systems.
- Self-Healing Concrete: Embedded microcapsules allow cracks to heal automatically, extending the lifespan of modular units.
These advancements improve not only the environmental performance of cement but also its adaptability to the rapid pace and precision of modular construction.
Case Studies: Cement in Action
Several successful projects have demonstrated the value of cement in modular construction:
- High-Rise Housing: In cities like Singapore and Hong Kong, precast concrete modules have been used to construct high-rise residential towers quickly and efficiently.
- Emergency Hospitals: During the COVID-19 pandemic, prefabricated concrete modules allowed for the rapid deployment of fully functional medical facilities in record time.
- Student Housing: University dormitories built using volumetric concrete modules provide affordable, robust accommodations with a fast return on investment.
These real-world examples highlight how cement enables the delivery of large-scale projects without compromising on quality or sustainability.
Challenges and Considerations
Despite its benefits, the use of cement in modular construction is not without challenges:
- Weight: Cement-based materials are heavier than steel or timber, which can increase transportation and handling costs.
- Carbon Footprint: Cement production is carbon-intensive. However, integrating supplementary cementitious materials (SCMs) or using alternative binders can mitigate this impact.
- Design Limitations: Precast components require careful planning and precise coordination during the design and manufacturing stages.
Addressing these issues requires a holistic approach that balances performance, sustainability, and logistics during both design and construction phases.
Future Outlook
The future of cement in modular construction is tied closely to trends in sustainability, digital design, and materials science. As digital tools like BIM (Building Information Modeling) become more integrated, cement components will be engineered with even greater precision and efficiency. The adoption of green cements and closed-loop material cycles will further enhance the ecological value of modular buildings.
In addition, collaborations between cement producers, modular manufacturers, and architects are driving innovation in panelization, assembly systems, and structural design. These partnerships will be critical in shaping the next generation of resilient and affordable structures.
Conclusion
Cement continues to be a versatile and indispensable material in modular construction systems. Its strength, durability, fire resistance, and adaptability make it an ideal choice for a wide range of modular applications — from affordable housing to high-end commercial projects. While sustainability and weight considerations must be managed, innovations in green cement and prefabrication techniques are addressing these concerns effectively.
As the demand for faster, greener, and smarter construction grows, the synergy between cement and modular technologies will define the future of building. By combining centuries-old materials with modern methodologies, the industry can deliver structures that are not only efficient and sustainable but also built to last.