Cement Slurry Applications in Oil Well Drilling
03.06.2025
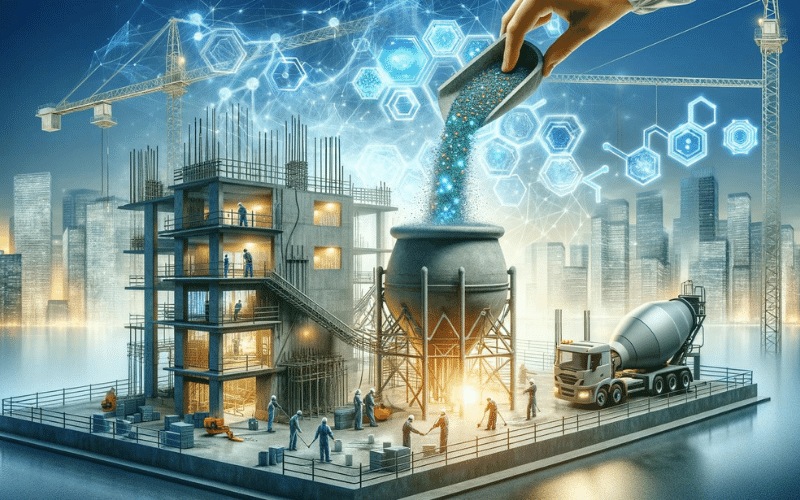
Introduction to Cement Slurry in Oilfield Operations
Cement slurry plays a vital role in the success and safety of oil well drilling operations. It is a fluid mixture of cement, water, and various additives designed to achieve specific performance characteristics. The primary objective of using cement slurry in oil well drilling is to seal the wellbore, isolate formation zones, and provide structural support to the casing.
As the energy industry continues to demand deeper wells and more complex drilling conditions, the importance of properly designed cement slurry becomes even more critical. This article explores the key applications, benefits, and technical considerations of cement slurry in oil and gas exploration.
1. Zonal Isolation
Zonal isolation is one of the most essential applications of cement slurry in oil well drilling. The slurry is pumped into the annular space between the well casing and the borehole wall to prevent fluid migration between geological formations. This isolation ensures that hydrocarbons do not flow into non-producing zones or contaminate freshwater aquifers.
By achieving a strong, impermeable seal, cement slurry helps maintain well integrity throughout the life of the well. A failure in zonal isolation can lead to production losses, regulatory violations, and costly remedial operations.
2. Structural Support for Casing
Another critical function of cement slurry is to provide mechanical support to the casing strings within the well. Once the cement sets, it helps anchor the casing in place and prevents movement under subsurface pressures. This structural integrity is essential during production, stimulation, and any future interventions.
Cement strength and density are carefully engineered to match the well’s depth and pressure conditions. Advanced slurries are often tested in labs to ensure they meet the required compressive strength and elasticity standards before use in the field.
3. Protection Against Corrosive Fluids
Subsurface formations can contain corrosive elements such as hydrogen sulfide (H₂S), carbon dioxide (CO₂), and saline water. These elements can deteriorate steel casing over time. Cement slurry acts as a protective barrier that shields the casing from corrosive attack.
Special additives are often included in the slurry design to enhance chemical resistance and increase the durability of the cement sheath. Long-term corrosion protection is key for ensuring the longevity and reliability of oil wells.
4. Preventing Blowouts and Well Control
Cementing operations contribute significantly to well control and safety. By sealing off high-pressure zones, cement slurry prevents uncontrolled flow of formation fluids to the surface, which can result in blowouts. Proper cementing is thus a fundamental component of a well’s blowout prevention strategy.
Additionally, during drilling pauses or plug-and-abandon operations, cement plugs are placed within the wellbore to temporarily or permanently isolate certain sections, ensuring well integrity and regulatory compliance.
5. Casing Equipment Stabilization
Cement slurry helps stabilize casing hardware such as centralizers, packers, and float collars. These components are crucial for maintaining alignment and spacing of the casing string. A solid cement sheath ensures that these tools function effectively under varying pressure and temperature conditions.
Inadequate cement placement around these components can lead to uneven load distribution and failure of the casing string or completion equipment.
6. Formation Integrity Testing
Cement slurry is also used in formation integrity testing (FIT) and leak-off tests (LOT) to evaluate the strength of the formation at the casing shoe. A cement plug is often set and allowed to cure before testing pressure is applied. This helps determine whether the formation can withstand the expected drilling pressures.
Accurate testing ensures the safety of the next drilling phase and prevents fracturing of weak formations, which can result in lost circulation and well control issues.
7. Plug and Abandonment Operations
When a well reaches the end of its productive life, it must be properly sealed and abandoned. Cement slurry is pumped into the well to create permanent barriers that prevent the migration of hydrocarbons to the surface or other formations.
Abandonment plugs are carefully placed and pressure-tested to meet stringent industry regulations. The long-term integrity of these cement plugs is essential for environmental protection and regulatory compliance.
Design Considerations for Cement Slurry
Successful cementing operations require a slurry that meets specific criteria such as pumpability, setting time, compressive strength, and resistance to high temperatures and pressures. Engineers use software simulations and laboratory testing to fine-tune the slurry composition.
Key additives include:
- Retarders: Delay the setting time for deep wells.
- Accelerators: Speed up setting in shallow or cold environments.
- Fluid loss agents: Prevent dehydration of slurry.
- Dispersants: Improve flowability and reduce viscosity.
- Extenders: Lower slurry density for weak formations.
Each component must be chosen based on subsurface conditions, such as temperature, pressure, and formation fluid chemistry.
Types of Cement Used in Oil Well Slurries
API (American Petroleum Institute) has standardized several classes of oil well cement. The most commonly used types include:
- Class A: For shallow wells with low-pressure conditions.
- Class G and H: Most widely used for moderate to high-depth wells.
- Pozzolanic cements: Add fly ash or silica for enhanced resistance.
These cements are often blended on-site or in bulk plants to match the exact specification of the slurry program.
Challenges and Troubleshooting in Cementing
Despite careful planning, field operations can encounter several challenges such as poor mud removal, channeling, or incomplete zonal isolation. These issues may arise due to improper centralization, loss of circulation, or early slurry setting.
To address these challenges, operators often use techniques like pre-flushes, spacers, and optimized displacement rates. Real-time monitoring during cementing operations helps identify deviations and adjust the process accordingly.
Innovations in Cement Slurry Technology
Recent advancements in cement slurry formulations include the development of self-healing cements, foam cement for high-gas formations, and nano-additive slurries for enhanced strength. Digital tools now allow for real-time data acquisition and performance monitoring during slurry placement.
These innovations help reduce non-productive time (NPT), minimize environmental impact, and improve long-term well performance. The future of oil well cementing lies in data-driven, adaptive, and sustainable technologies.
Conclusion
Cement slurry is an indispensable material in oil well drilling, offering a wide range of applications from structural support to zonal isolation and environmental protection. Its proper design, application, and monitoring ensure the long-term integrity and safety of oil wells across various geological conditions.
As drilling environments become more complex, the industry must continue to innovate and refine cementing practices. With advanced materials, smart technologies, and rigorous safety protocols, cement slurry will remain a cornerstone of efficient and safe oilfield development.