Cement Coatings for Anti-Corrosion in Marine Environments
24.06.2025
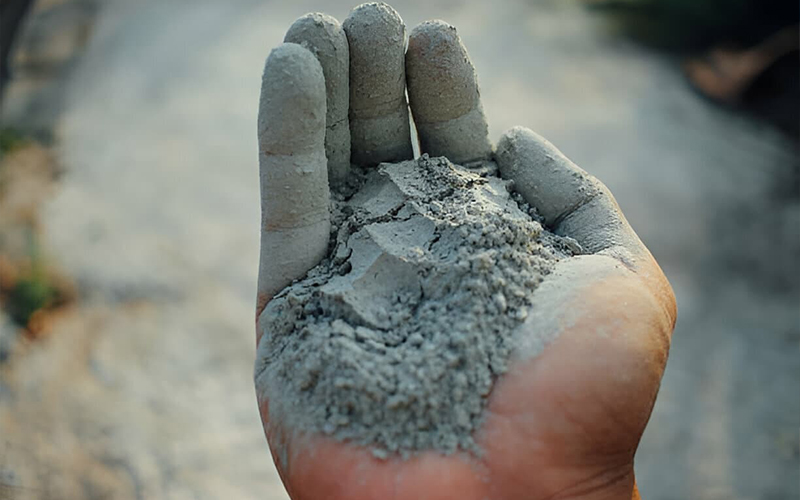
The Challenge of Corrosion in Marine Infrastructure
Marine environments present one of the most aggressive conditions for infrastructure, especially those involving steel reinforcements or metallic elements. Constant exposure to saltwater, humidity, and fluctuating temperatures accelerates corrosion processes, threatening the integrity and lifespan of marine structures. To combat this, cement-based coatings have emerged as a reliable and cost-effective solution for anti-corrosion protection.
From offshore platforms to harbors, underwater pipelines to seawalls, every marine structure requires protective strategies. Cement coatings provide a physical and chemical barrier that reduces the ingress of chlorides and moisture — two of the primary drivers of corrosion in marine zones. Their compatibility with both concrete and steel makes them a preferred material in coastal engineering.
What Are Cement-Based Anti-Corrosion Coatings?
Cement coatings are specially formulated mortar or slurry mixtures applied as a protective layer over substrates like steel or concrete. These coatings often contain additives such as polymers, microsilica, or corrosion inhibitors to enhance their performance. Once applied, they cure into a dense, durable surface that resists water, salts, and chemical reactions.
Unlike organic coatings such as epoxies, cement-based coatings offer breathability while maintaining impermeability to harmful agents. They also exhibit excellent adhesion, mechanical strength, and compatibility with marine construction materials, allowing them to act both as a barrier and a bonding layer in structural applications.
Why Use Cement Coatings in Marine Settings?
The choice of cement coatings in marine environments stems from their unique advantages:
- Chloride Resistance: These coatings limit the penetration of chloride ions, which are the main culprits behind rebar corrosion.
- Alkalinity Preservation: Cement maintains the alkaline environment around reinforcement bars, helping to keep steel in a passivated (non-corroding) state.
- Structural Compatibility: Cement coatings expand and contract similarly to concrete, minimizing the risk of cracking and delamination.
- Environmental Durability: They can withstand wet-dry cycles, seawater spray, and tidal action over extended periods.
For infrastructure that must endure for decades in coastal or submerged conditions, these features are critical to long-term performance and safety.
Common Applications of Cement Coatings in Marine Projects
Cement coatings are used across a variety of marine and coastal structures, including:
- Bridge Piers and Foundations: To prevent corrosion of steel reinforcements in splash zones and underwater segments.
- Seawalls and Docks: To protect exposed concrete from salt intrusion and wave impact.
- Steel Piles and Sheet Piling: Where cementitious coatings form a protective jacket, isolating metal from corrosive environments.
- Water Intake Structures: Such as those used in power plants or desalination facilities, often coated to prevent deterioration due to salt exposure.
These applications benefit from the robust protection and low maintenance offered by cement coatings, reducing repair frequency and operational disruptions.
Types of Cement-Based Anti-Corrosion Systems
There are several formulations of cement coatings designed for specific performance outcomes in marine zones:
- Polymer-Modified Cementitious Coatings (PCC): These coatings have enhanced adhesion and flexibility, ideal for surfaces that undergo movement or thermal expansion.
- Mineral-Based Corrosion Inhibiting Coatings: Incorporate compounds like calcium nitrite to actively neutralize corrosion reactions on steel surfaces.
- High-Density Micro-Silica Coatings: Use fine particles to produce a denser matrix that blocks chloride and moisture penetration.
The selection depends on factors such as exposure severity, substrate type, and application method, ensuring optimal results for each project.
Application Methods and Surface Preparation
Proper surface preparation is essential for the success of cementitious anti-corrosion coatings. Concrete or steel surfaces must be clean, free of loose particles, and ideally roughened to enhance mechanical bonding. For steel, sandblasting is commonly used to achieve an appropriate anchor profile.
Coatings are typically applied using brush, trowel, or spray equipment, depending on thickness and accessibility. Curing is a critical step to ensure the development of proper strength and adherence. In some marine applications, the coating process may occur in dry docks before installation or as part of maintenance operations in the field.
Performance Metrics and Testing
To ensure reliability, cement coatings for marine environments are tested for various performance characteristics:
- Chloride Diffusion Resistance: Determines how effectively the coating blocks salt ion penetration.
- Adhesion Strength: Measures how well the coating adheres to concrete or steel substrates under stress.
- Water Permeability: Low permeability ensures reduced water ingress and corrosion risk.
- Freeze-Thaw Resistance: Assesses durability under changing temperature cycles common in marine climates.
These tests help verify product suitability for specific environmental conditions and structural requirements.
Case Studies in Marine Corrosion Protection
Numerous successful projects demonstrate the effectiveness of cement-based coatings. For example, the repair of submerged bridge piers in the Gulf Coast involved polymer-modified cement coatings that restored both structural strength and corrosion resistance. Similarly, harbor walls in Scandinavia were rehabilitated using spray-applied micro-silica cementitious coatings, which extended their lifespan despite harsh freeze-thaw and salt exposure.
Another notable application was on steel sheet piles along a major canal, where cementitious mortar jackets were used to prevent tidal corrosion. These solutions not only delayed expensive replacements but also improved safety and function in critical infrastructure areas.
Sustainability and Environmental Benefits
Cement coatings also contribute to environmental sustainability in marine construction. Unlike organic coatings that may release volatile organic compounds (VOCs), cement-based systems are inert and eco-friendly. Many of these products incorporate recycled materials or low-carbon cement blends to reduce environmental impact.
Moreover, extending the lifespan of marine structures reduces the need for frequent reconstruction, conserving resources and minimizing disruption to marine ecosystems. In this way, cement coatings serve both protective and ecological functions.
Limitations and Considerations
While cement coatings are highly effective, they are not suitable for every scenario. In extremely dynamic underwater environments with strong mechanical abrasion, additional protective layers or hybrid systems may be necessary. Improper application or insufficient curing can also lead to coating failure.
Therefore, professional assessment and execution are crucial to ensure coating performance. Engineers must evaluate structural conditions, corrosion risk, and exposure level before specifying the right system.
Conclusion: Cement Coatings as a Long-Term Anti-Corrosion Solution
Cement coatings offer a proven, sustainable, and durable solution for protecting marine infrastructure from corrosion. Their ability to form an effective barrier against saltwater, combined with excellent bonding and structural compatibility, makes them an essential part of modern marine engineering.
As coastal development increases and aging infrastructure demands more maintenance, cement-based anti-corrosion systems will continue to play a vital role. With proper application and formulation, these coatings not only extend the life of marine structures but also support safer, more resilient coastal environments for the future.